Senior Engineer, Mechanical
ADNOC Group
Date: 3 weeks ago
City: Abu Dhabi
Contract type: Full time
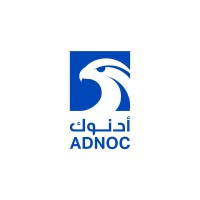
About The Company
ADNOC Distribution is on a journey to change the retail landscape, delivering tangible actions to facilitate progress in providing sustainable mobility solutions for our customers. We are taking bold and transformative steps to grow our domestic and international footprint for our customers. We are customer-centric, offering digitally enabled journeys and providing innovative products and services to drive accelerated and sustainable development for the future of mobility.
ADNOC Distribution markets, sells, and distributes transportation fuel to both retail and commercial customers. We also run non-fuel services at our service stations.
Job Purpose
Lead and ensure optimized resources, and downtime for all mechanical equipment, and major activities minimizing variations or impact on business continuity for 10 Depots, 2 Plants, and 547 Fuel Service Stations. Develop and implement systems and procedures for mechanical systems for continuous operational performance improvement across the site and extend continuous support post-handover of new facilities. Provides expert engineering technical support on activities such as maintenance, troubleshooting, repair, overhaul and shutdowns to maintain static and rotating equipment effectively and efficiently to achieve high degree of availability, reliability and integrity and to ensure that mechanical equipment, piping, structure tools and machinery of facilities are operated and maintained in line with best world-class practices and standards.
Key Accountabilities
Maintenance Planning, Execution and Expertise
ADNOC Distribution is on a journey to change the retail landscape, delivering tangible actions to facilitate progress in providing sustainable mobility solutions for our customers. We are taking bold and transformative steps to grow our domestic and international footprint for our customers. We are customer-centric, offering digitally enabled journeys and providing innovative products and services to drive accelerated and sustainable development for the future of mobility.
ADNOC Distribution markets, sells, and distributes transportation fuel to both retail and commercial customers. We also run non-fuel services at our service stations.
Job Purpose
Lead and ensure optimized resources, and downtime for all mechanical equipment, and major activities minimizing variations or impact on business continuity for 10 Depots, 2 Plants, and 547 Fuel Service Stations. Develop and implement systems and procedures for mechanical systems for continuous operational performance improvement across the site and extend continuous support post-handover of new facilities. Provides expert engineering technical support on activities such as maintenance, troubleshooting, repair, overhaul and shutdowns to maintain static and rotating equipment effectively and efficiently to achieve high degree of availability, reliability and integrity and to ensure that mechanical equipment, piping, structure tools and machinery of facilities are operated and maintained in line with best world-class practices and standards.
Key Accountabilities
Maintenance Planning, Execution and Expertise
- Manage and participate for review of Mechanical Layouts, Specifications, SAFOP / E-HAZOP, Operability and Maintainability studies, participate in workshops and design and plot plan reviews and contribute with site requirements and experience towards improvement of existing systems as required.
- Review and contribute to studies of the adequacy of the system and recommend system upgrades/changes to meet operational and maintenance challenges.
- Ensure effective and timely support in the areas of technical performance issues such as reliability, availability, integrity and analysis of performance gaps involving equipment failure.
- Develop scope of work for major overhauls of electrical equipment & work service orders and mini projects. coordinate implementation with other Sections.
- Carry out technical assessment of bid documents for services and material required for the works. Participate in clarification meetings with contractors and vendors to ensure compliance with technical specifications & requirements. Preparation of Technical Evaluation and appraisal reports.
- Review the update technical drawings for the installations and ensure conformity of the as-built status with the Design and Technical requirements.
- Provide effective interfaces and relationships within/between disciplines, site teams and peers in other site project teams.
- Network and deliver progress reports, proposals, requirements documentation and presentations to Site team or interface teams and other Project owners for fast tracking projects.
- Improve equipment performance by efficient application of condition-based maintenance techniques.
- Provides technical expertise with experience-based knowledge and assistance to site maintenance departments.
- Participates in reliability studies for Brownfield/Greenfield equipment to help the maintenance department review practices, philosophies, and strategies. Advises maintenance support on troubleshooting non-routine equipment failures, root cause analysis, and reliability audits as needed.
- Lead and direct the major electrical activities to be carried out with the operation/maintenance targets KPI’s being achieved or exceeded.
- Consolidate, discuss and review requirements and participate as required in Design Technical Review Meetings, Site Surveys, and Factory Acceptance Tests, Site Acceptance Tests and installation, commissioning and handover activities.
- Critically review major works related Equipment, Procedures, Spare Parts, documentation etc. are set up and kept properly updated and handed over post works.
- Oversee the commissioning and hand-over of new facility. Highlight and address maintenance, operational, design and warranty/guaranty related issues with stakeholders.
- Assist in troubleshooting and Liaise with vendor /support teams post major works for support to minimize equipment downtime after any malfunction or failure or breakdown
- Periodic follow-up all punch list items until completion with engineering and execution teams with proper prioritization and timeframe for the actions.
- Assist and follow-up for the mechanical control system activities and actions plans as required by site operations team.
- Maintain and develop the engineering and technical solutions to improve reliability performance of electrical equipments and system.
- Recommends and identifies training requirements to ensure up to date and functional knowledge base.
- Coordinate, follow-up and prepare in-house activities, major projects and campaigns shutdown requirements with support units and contractor for minimum operational interventions and shutdowns within site resource limitations, in line to company objectives.
- Oversee predictive/ Reliability Centered Maintenance (RCM) programs for condition monitoring of mechanical equipment to ensure improved machine availability and reliability.
- Develop and optimize vendor, OEM and specialist contractor support and arrange specialist services.
- Participates in maintenance planning by reviewing/reporting anticipated future requirements of overhauls, maintenance, repairs, spare parts.
- Study and carry out residual life assessment of critical electrical equipment and suggest corrective action to be initiated by respective area engineers.
- Conduct site engineering study to determine the feasibility of introducing modification to increase reliability and efficiency of the plant.
- Provide technical input to update company specifications to incorporate the latest industry trends and company’s lessons learned.
- Lead the activities of troubleshooting and analysis of complex engineering problems and offer effective resolutions to ensure that maintenance services are provided safely and efficiently.
- Witness factory and site acceptance tests, pre-commissioning and commissioning of equipment/ systems and assures that the installation and performance are in accordance with specifications and approved for construction documents.
- Maintain mechanical equipment in line with HSECES guidelines and ensure compliance to Minimum Assurance Tasks requirements.
- Carry out periodical review and advise on updating material stock and directs supervision of specifications considering information from manufacturers including deletion, obsolete and incorporation of new items, ensure availability of spares and materials.
- Closely monitor mechanical contractor activities, by conducting audit and weekly meeting to highlight their shortfalls, drawbacks and suggests improvement for the effective implementation of scope in line with the Service Agreements.
- Diagnose, analyse, and carry out root cause failure analysis, highlight reasons for equipment failure and advise on remedial measures to avoid failures. Also, to study and carry out residual life assessment of critical mechanical equipment and suggest corrective action to be initiated by respective area engineers.
- Monitor and analyse failure reports, identify bad actors (RCA) and initiate corrective actions and develop solutions to rectify the problems and improve the performance.
- Ensure the availability and reliability of mechanical system/ equipment, and the smooth integration of new facilities such as modification/ upgradation of existing and additional facilities. Conduct site engineering studies to determine the feasibility of introducing, modification and incorporate the same to increase reliability and efficiency.
- Study and carry out residual assessment of critical mechanical equipment and suggest corrective action to be initiated by respective maintenance departments/ teams.
- Develop scope of work for major overhauls of mechanical equipment and work service orders and mini projects, coordinate implementation with other departments/ teams.
- Develop and optimize vendor, OEM and specialist contractor support and arrange specialist services.
- Carry out technical evaluation of bids related to service work orders and service agreements.
- Evaluate and ensure that the contractor designs are in accordance with the scope of work and facilities delivered to end user are safe, reliable, operable, and maintainable.
- Develop comprehensive monthly and annual management information system report covering all the major activities of the section, including expenditure profile and prepare various other presentation reports as and when required.
- Coordinate with Projects Division for any studies/ site related issue and project scope development.
- Oversee predictive/ Reliability Centered Maintenance (RCM) programs for condition monitoring of mechanical equipment to ensure improved machine availability and reliability.
- Develop and apply engineering standards and procedures to assure adherence to industry norms and corporate policies, set up and use engineering standards both domestically and internationally, ensuring that all mechanical systems are created and implemented in accordance with codes and standards set by the industry.
- Lead, coach, and mentor electrical maintenance supervisors and technicians within the maintenance division to ensure the enhancement of their technical capabilities and to provide them with the needed technical direction and support.
- Conduct design assessments and suggest enhancements in accordance with industry best practices and cutting-edge technologies.
- Accountable for examining designs and recommending changes considering new technologies and recommended procedures, including the reviewing of design concepts, analysing new products and technology, and suggesting changes.
- B. Sc. Degree in Mechanical Engineering or equivalent Professional Qualification.
- Minimum 10 years’ experience in mechanical maintenance engineering of rotating and static equipment, preferably in the Oil and Gas industry.
- In-depth working knowledge on principles related to rotating and static equipment used in Oil and Gas Plants.
- Experience in the execution of equipment maintenance of diverse metal crafts including machine tooling, bench fitting, fabrication, welding, rigging, repair, etc. Working background on different mechanical tools.
- Good knowledge about monitoring and predictive maintenance programs associated with mechanical systems.
- Excellent knowledge about specifications, codes, and standards for rotating and static equipment. Good knowledge about mechanical safety requirements and HSE procedures and practices.
- Good Knowledge of RCA process, RCM methodology, Bad actor Identification process.
- Planning and organizing, scheduling, and coordinating, checking, examining, and recording.
- Understanding and knowledge of RAM process methodology to support design, production and product development.
- Understanding and knowledge of engineering data (e.g., blueprints, data sets, specifications, diagrams, schematics) to interpret, analyze, and develop data for support requirements.
How to apply
To apply for this job you need to authorize on our website. If you don't have an account yet, please register.
Post a resumeSimilar jobs
Technical / Design Manager - Infrastructure
AtkinsRéalis,
Abu Dhabi
8 hours ago
AtkinsRéalis are looking for a Technical / Design Manager - Infrastructure in Abu Dhabi, UAE.About AtkinsRéalisCreated by the integration of long-standing organizations dating back to 1911, AtkinsRéalis is a world-class engineering services and nuclear company dedicated to engineering a better future for our planet and its people. We create sustainable solutions that connect people, data and technology to transform the...
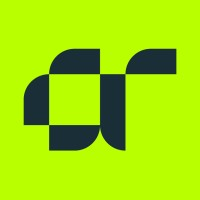
Senior Principal Resident Engineer (Water Transmission and Distribution Projects)
Parsons Corporation,
Abu Dhabi
23 hours ago
In a world of possibilities, pursue one with endless opportunities. Imagine Next!When it comes to what you want in your career, if you can imagine it, you can do it at Parsons. Imagine a career working with intelligent, diverse people sharing a common quest. Imagine a workplace where you can be yourself. Where you can thrive. Where you can find...
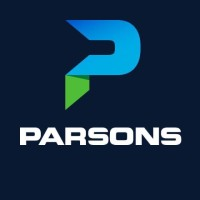
Senior Program Manager - Cybersecurity
Help AG, an e& enterprise company,
Abu Dhabi
1 day ago
Help AG is looking for a highly experienced and strategic Program Manager to oversee a portfolio of complex Cybersecurity projects within a very large-scale enterprise environment. The ideal candidate will be responsible for ensuring program oversight, governance, vendor coordination and executive reporting of multiple concurrent initiatives, while aligning with organizational goals and scope. This role requires strong leadership, stakeholder management,...
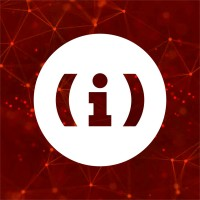